Al-Si-Mg系铸造铝合金因其优异的铸造性能和耐腐蚀性能而广泛应用于汽车和航空航天领域。然而,铁作为铝合金铸件生产过程中不可避免的杂质元素之一,其在铝中的最大溶解度仅为0.05 wt.%,极易与其他元素形成粗大的脆性金属间化合物(主要是π-Fe相—Al8Mg3FeSi6),严重降低合金的综合力学性能。因此,有害π-Fe相的调控成为了全面提升材料性能的关键。
固溶处理是改善合金中含铁金属间化合物形貌的主要方法之一。研究表明,当Mg含量较低(< 0.5 wt.%)时,传统固溶处理过程中Mg2Si相分解释放的Mg原子难以满足α-Al基体中Mg饱和固溶的要求。因此,π-Fe相也要通过转变成β-Fe(Al5FeSi)相来提供Mg原子,从而可实现含Fe相的形貌调控。一般来说,随着合金中Mg含量的增加,可用做强化的Mg2Si相越多,合金的屈服强度会不断提高。因此,强度指标要求较高的铸件往往需要具有较高的Mg含量。然而,对于高Mg含量(Mg > 0.5wt.%)的Al-Si合金,传统单级固溶处理往往面临“顾此失彼”的困境——低温处理无法有效改善π-Fe相的形态,而高温处理又可能导致合金过烧。这一矛盾促使研究者寻求更精细化的相调控策略。
大连理工大学“辽宁省凝固控制与数字化制备技术重点实验室”科研人员以高Mg含量的Al-7Si-0.6Mg合金为研究对象,首先分析了其在传统单级固溶处理过程中微观组织的变化。结果表明,在低温(540℃)固溶处理条件下,即使固溶时间长达20 h,组织中的π-Fe相仍保持粗大的汉字状形态(图1和图2);560℃高温固溶可将粗大汉字状π-Fe相转变成细小颗粒状β-Fe颗粒(图3),但是组织发生过烧。因此,简单的单级固溶处理难以有效调控π-Fe相。基于铸态及固溶态合金热稳定性(图4)研究,研究团队提出了两段式固溶处理的策略(540℃ × 8 h + 560℃ × 4 h);在实现π-Fe相形貌控制的同时,避免组织的过烧风险(图5)。研究中首次观察到铸态组织中π-Fe相的三维空间形貌,其粗大的分支结构严重分割α-Al晶粒;经两段式的双级固溶处理后,π-Fe相形态由连续网状转变为颗粒状(图6)。这种显微组织的优化使合金获得强度与延展性的同步提升,突破了传统材料“强度-韧性权衡”的瓶颈(图7)。该策略为Al-Si-Mg合金的性能优化提供了可直接产业化的处理工艺,其“分步调控”的研究思路也为其他多相合金体系的组织调控设计提供了重要借鉴。
相关研究成果以“Modification of detrimental π-Fe phase in Al-7Si-0.6Mg alloy”为题发表在J. Mater. Sci. Technol. 240 (2026) 313-322上。
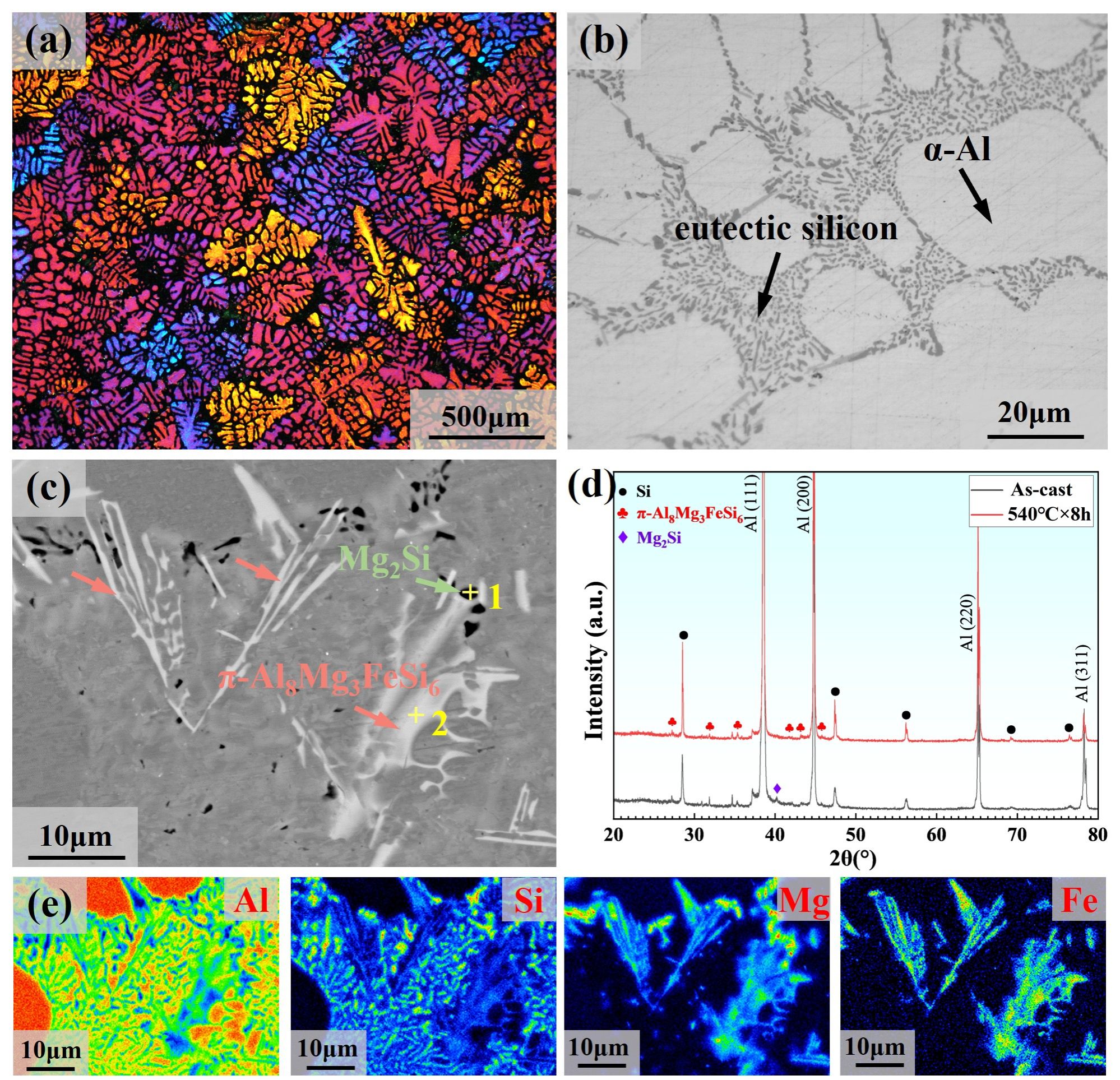
图1 Al-7Si-0.6Mg合金的铸态组织:(a) 偏光金相照片;(b) 金相照片;(c) 汉字状π-Fe相;(d) XRD图谱;(e) c图的EPMA面分析
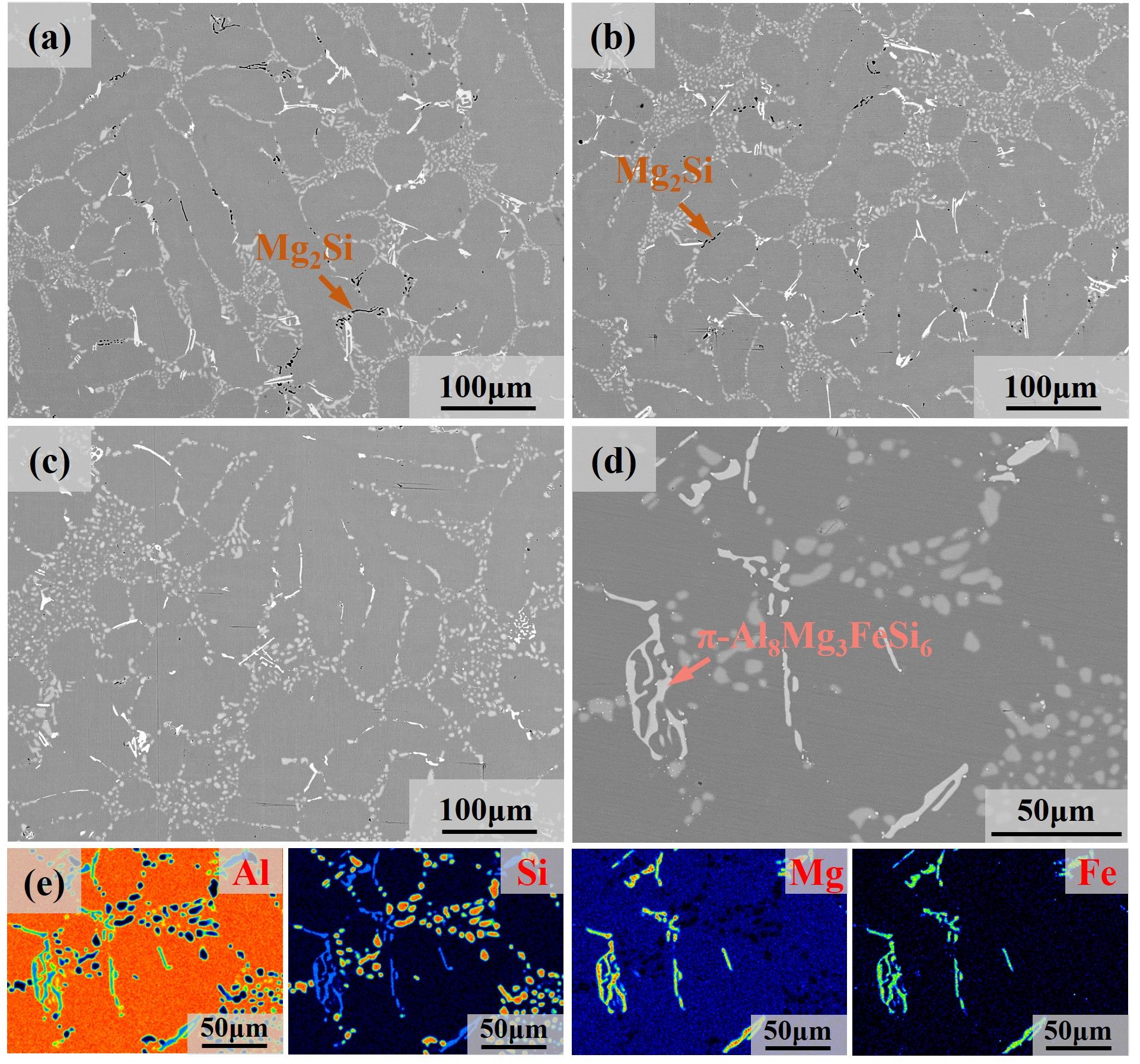
图2 540℃固溶处理过程中含Mg相的演变:(a) 1 h;(b) 2h;(c) 8h;(d) 20h;(e) d图的EPMA面分析
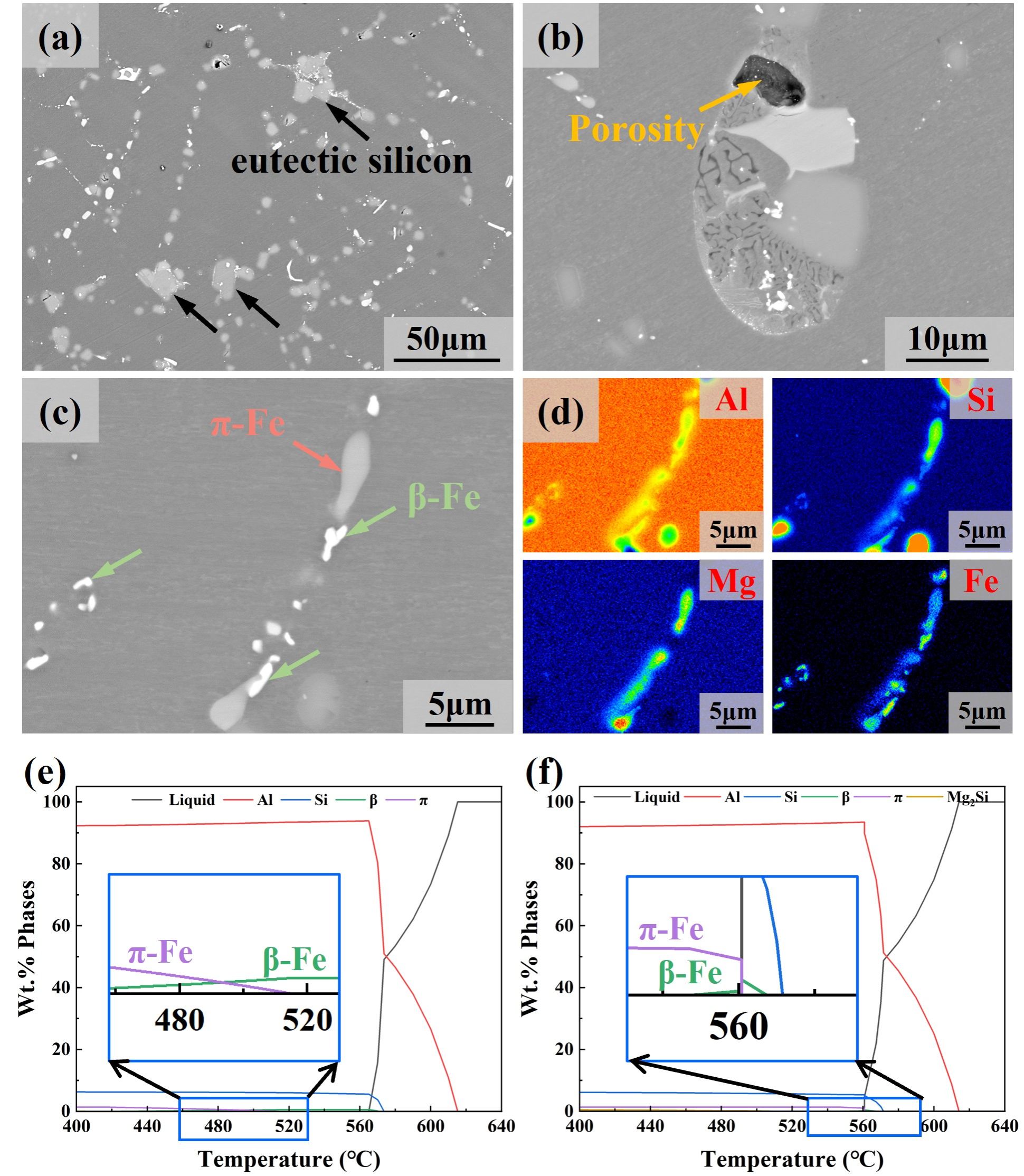
图3 560℃固溶处理2h后合金的显微组织:(a) 异常长大的共晶硅;(b) 复熔球;(c) π-Fe向β-Fe的转变;(d) c图的EPMA面分析;及不同Mg含量合金的相稳定性分析:(e) Al-7Si-0.3Mg-0.15Fe;(f) Al-7Si-0.6Mg-0.15Fe

图4 铸态合金及其经540°C固溶处理8h后的DSC曲线
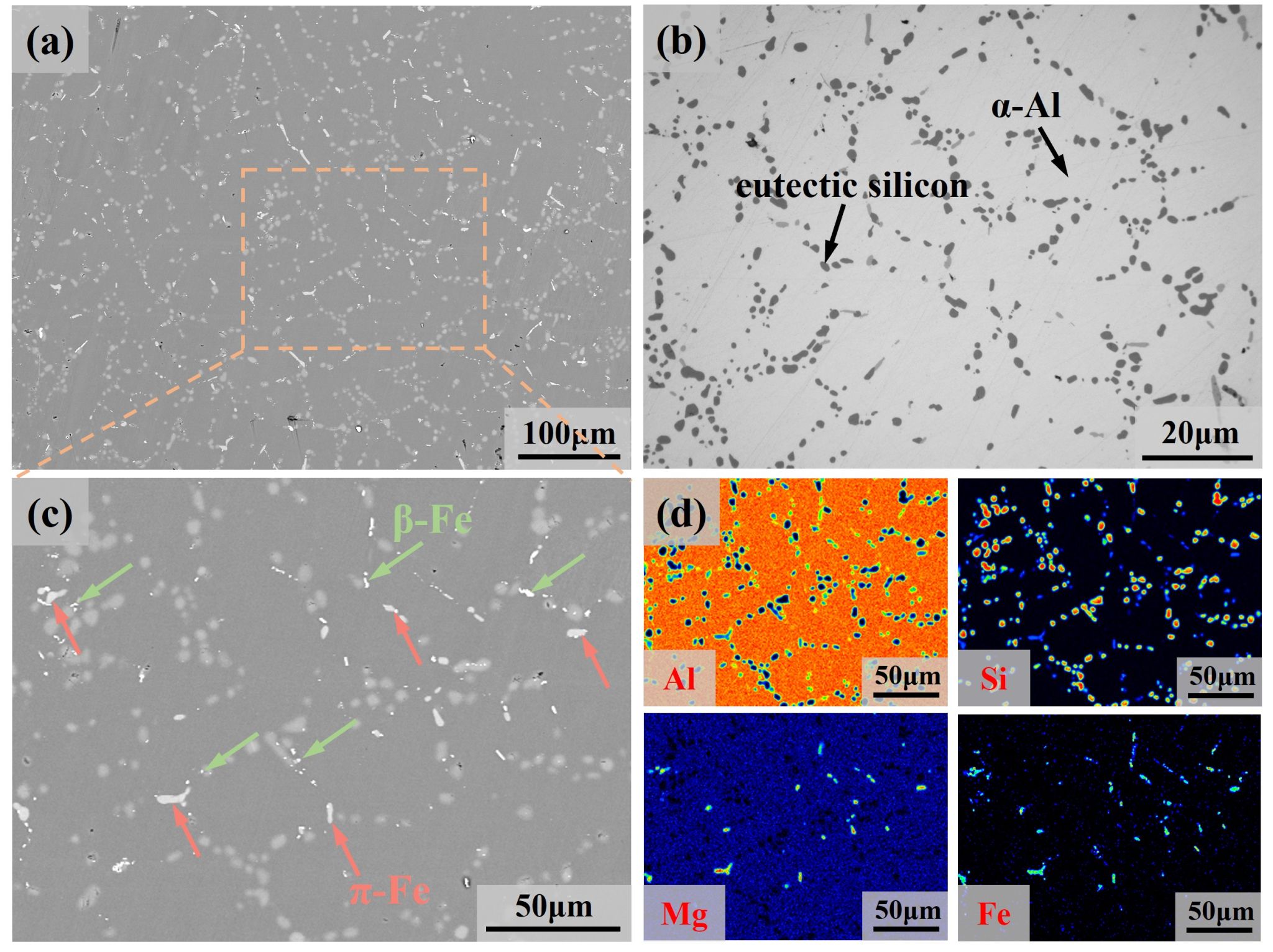
图5 双级固溶处理(540℃× 8 h + 560℃× 4 h)后合金的显微组织:(a) 低倍背散射照片;(b) 金相照片;(c) a图中虚线框区域的放大图;(d) c图的EPMA面分析
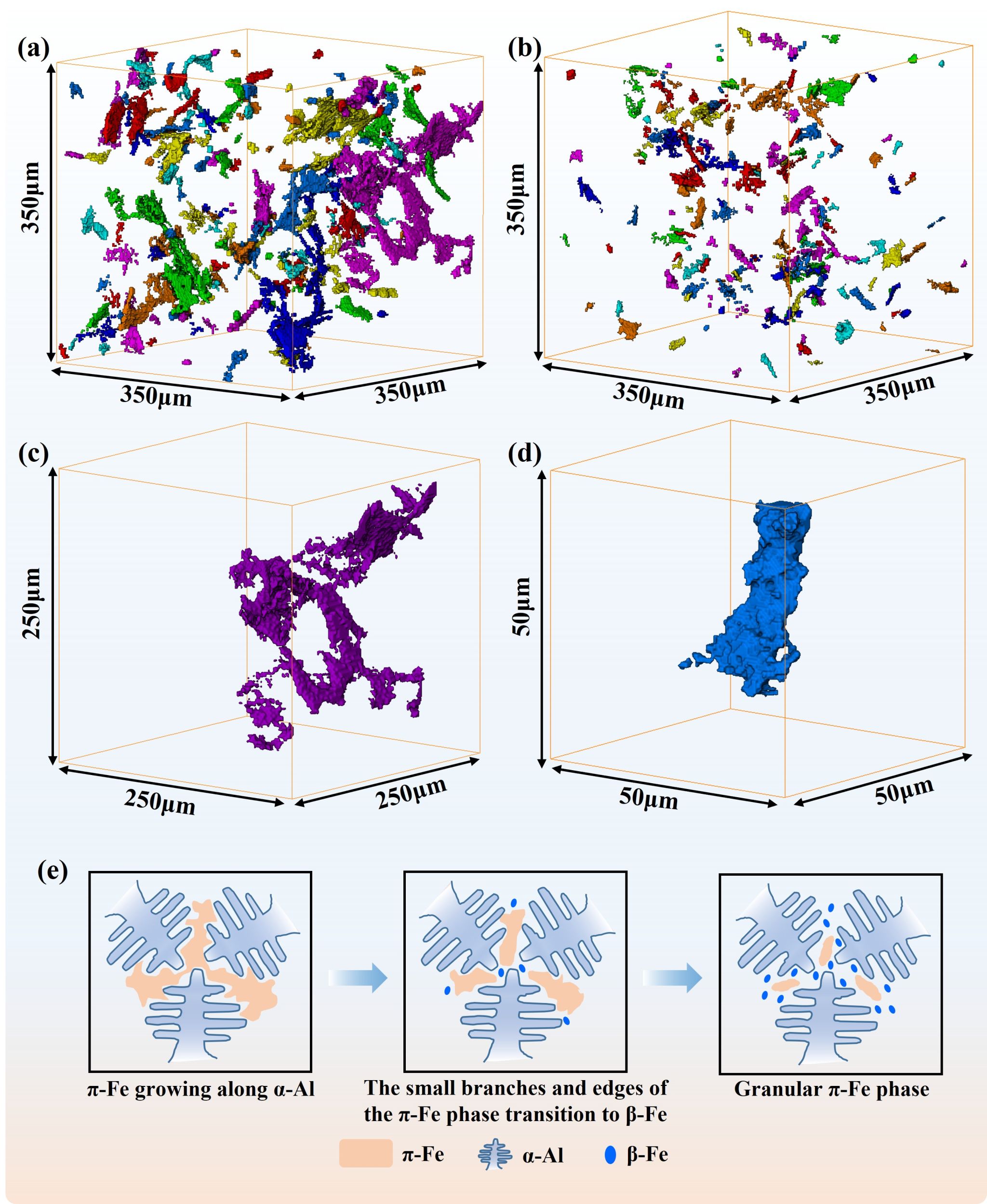
图6 不同固溶处理后合金中π-Fe相的三维形貌及其转变示意图:(a, c) 540°C × 12h;(b, d) 540°C × 8h + 560°C × 4h;(e) π-Fe相的转变示意图
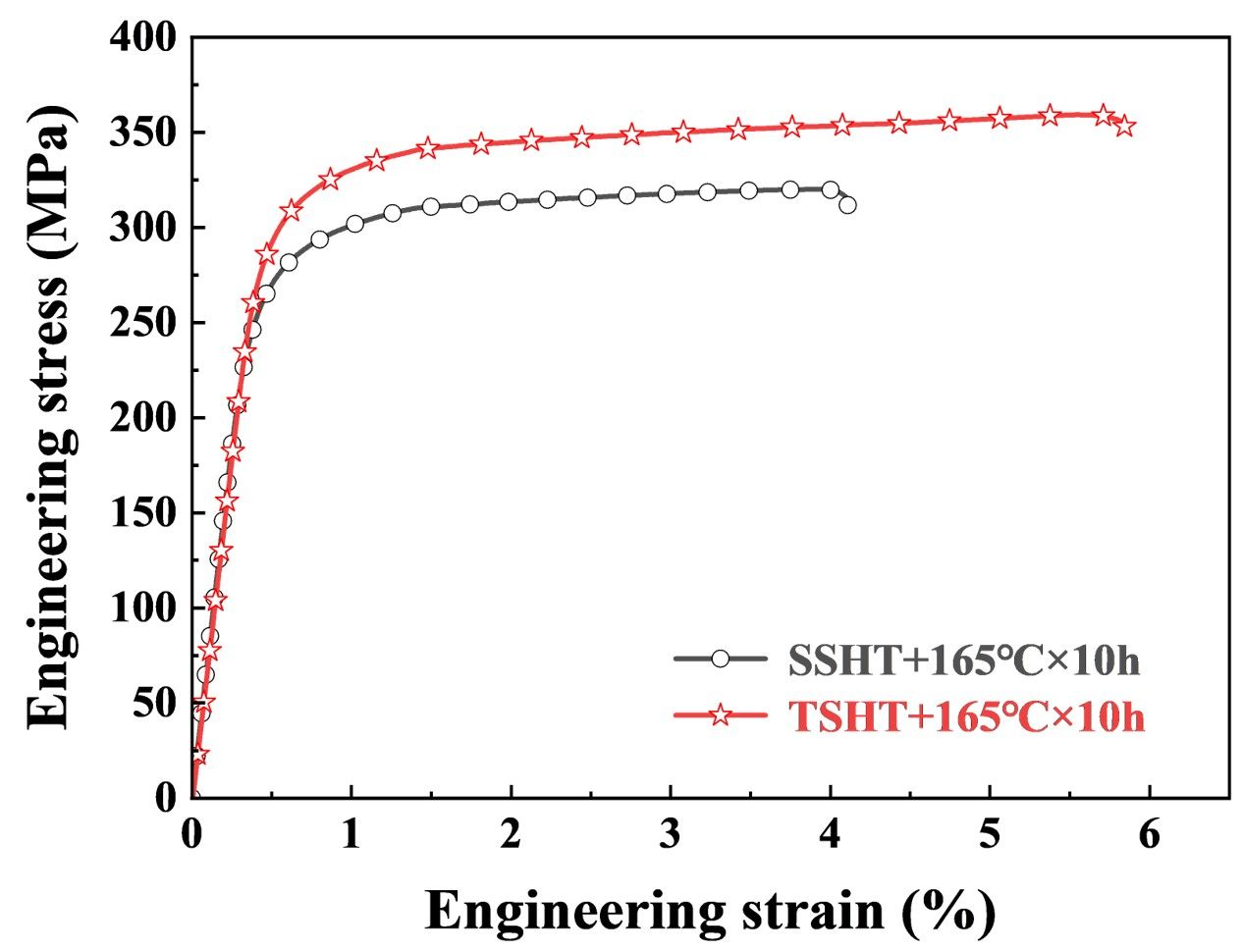
图7 合金经不同固溶处理后峰时效态的力学性能
论文链接:https://doi.org/10.1016/j.jmst.2025.01.091